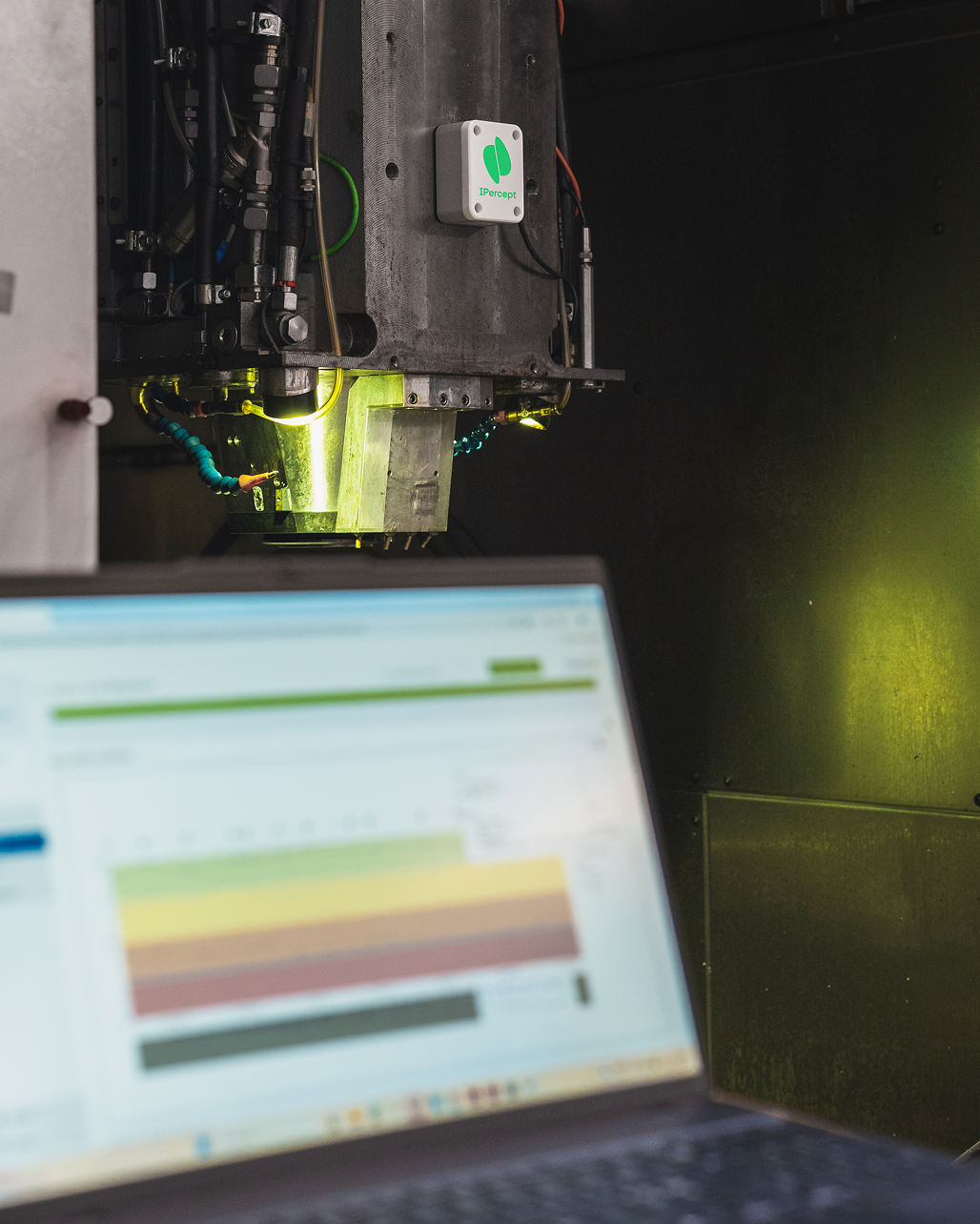
Konecranes Machine Tool Service (MTS), the leading machine tool service provider in Finland, is extending its offering with IPercept’s Fitness Tracker for Industrial Machines. Launched in May, the solution - branded as Smart Monitoring - is already transforming how production and maintenance teams operate.
Here are four real-world use cases demonstrating the impact:
1. Proactive Action on Spindle Bearing Failure
Application: 5-axis milling machine | Mining industry
Smart Monitoring detected a sudden degradation in bearing condition following a collision. It then tracked the decline until the bearing entered accelerated degradation - enabling a planned replacement with minimal production impact, and avoiding a likely critical failure.
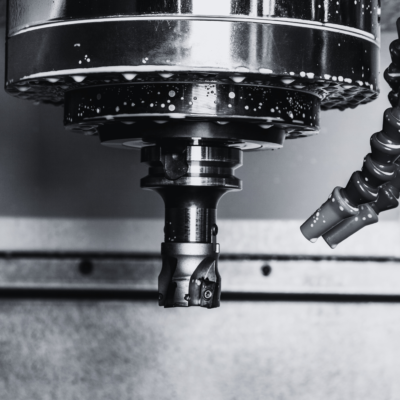
2. Loop Test for Abnormality Identification
Application: 5-axis milling machine | Automotive industry
The Smart Monitoring Loop Test identified a localized defect on one axis. Further investigation confirmed a dent in the ball-screw grooves. The defect was continuously monitored, allowing early planning of repairs before significant machine impact.
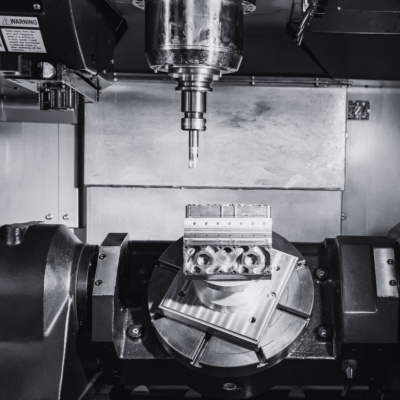
3. Ballscrew Replacement
Application: 5-axis milling machine | Automotive industry
Smart Monitoring revealed critical degradation in a ball-screw drive’s axial mount. It also tracked how the issue began affecting other components. After the replacement, Smart Monitoring confirmed improved system health and provided insights into the effectiveness of the repair.
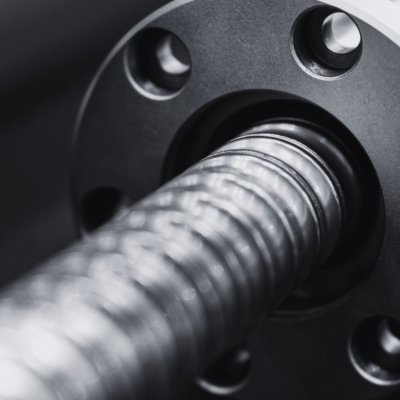
4. Prioritization and Optimization of Machine Park
Application: High-precision multi-op machines | Component manufacturing
Smart Monitoring evaluated an entire machine park, resulting in a targeted renovation program. One machine was decommissioned without productivity loss, and the expected lifetime of others was extended by over three years.
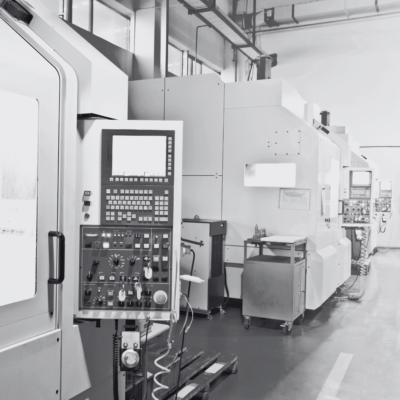
Want to learn more?
Visit the full Smart Monitoring overview on Konecranes' website: Konecranes Smart Monitoring | Konecranes Suomi